Z-Poxy finishing resin ..?
#1
Senior Member
Thread Starter
Join Date: Dec 2001
Location: Queensland, AUSTRALIA
Posts: 525
Likes: 0
Received 0 Likes
on
0 Posts

I have a small project ahead involving making a new cowling for my GWS foamy FW-190. I have made up a plug using polyurethane foam and applied four layers of nylon stocking over that. I`ve used this method before quite successfully - so far, so good.
I intend to use Z-Poxy finishing resin from a part-used pack that has been lying around for the past 2 - 3 years. It`s winter down here and the resin in the pack is very thick - like treacle. I don`t know whether this is all because of the cooler weather or its old age.
There is no way that I will be able to effectively apply this through the four layers of nylon in its present viscosity. I have sat the two packs of resin and hardener out in the sun for about an hour and it is obviously more fluid now as a result.
Before I head off to try it, can someone advise whether I can alternatively, or additionally thin this material before use. I did read somewhere that it can be thinned using acetone on a third, third, third ratio, but have no experience at all with this.
Has anyone had any experience with thinning this stuff and able to provide any advice?
Thanks,
Alan W
I intend to use Z-Poxy finishing resin from a part-used pack that has been lying around for the past 2 - 3 years. It`s winter down here and the resin in the pack is very thick - like treacle. I don`t know whether this is all because of the cooler weather or its old age.
There is no way that I will be able to effectively apply this through the four layers of nylon in its present viscosity. I have sat the two packs of resin and hardener out in the sun for about an hour and it is obviously more fluid now as a result.
Before I head off to try it, can someone advise whether I can alternatively, or additionally thin this material before use. I did read somewhere that it can be thinned using acetone on a third, third, third ratio, but have no experience at all with this.
Has anyone had any experience with thinning this stuff and able to provide any advice?
Thanks,
Alan W
#2

My Feedback: (6)

Alpha Whisky, my advice would be to mix up a small amount to see if it still gets hard. Then if it does what i normally do to thin it out is to mix a batch of the resin & hardner 50/50 and then put about two cap fulls of denatured alchohol in it and mix it till it is fully blended together and then use a disposable foam paint brush to apply it to the surface of what it is you are glassing just don't apply a whole lot just enough to wet the surface and it will penetrate thru the material pretty easy. It might require two or three coats to fill the weave of the material that you are glassing but it's pretty straight forward.
#4

My Feedback: (9)
Join Date: Feb 2003
Location: Akron,
OH
Posts: 234
Likes: 0
Received 0 Likes
on
0 Posts

I've had good luck microwave diffeant epoxies. Just nuke both bottles, with their tops off for about 20 seconcds. It will thin them down to a water like consitancy, however the kick off time is much, much quicker. 30 minute epoxy is down to about 5 minutes, Finishing resin should be good for about 10 minutes working time. If you spread it out on a paper plate as you use it it will last longer.
Jeff
Jeff
#6
Senior Member

When I'm working in a cold cellar during the winter ,I'll store
the Z-poxy upstairs in the warmer temps. I'll bring it into my
shop only to mix and spread it. To keep it flowing I'll use
my Monokote gun.
Good luck,
Roby
the Z-poxy upstairs in the warmer temps. I'll bring it into my
shop only to mix and spread it. To keep it flowing I'll use
my Monokote gun.
Good luck,
Roby
#7
Member
Join Date: Jul 2007
Location: Bowmanville,ON ON, CANADA
Posts: 71
Likes: 0
Received 0 Likes
on
0 Posts

AlphaWhisky
You can thin the z-poxy with 99% isopropyl alcohol available at your local pharmacy. I have been thinning with this for years.
The ratio is 1:1:1. The beauty of using alcohol is that it thins but evaporates off without affecting the resin.
I would not not use the acetone for anything other than clean -up. Although I even use the alcohol for cleaning my epoxy brush.
Try not to use the 70% iso alcohol. Too much water.
The other advantage to iso alcohol is if you have any cuts on your hands they get disinfected - LOL!
ByronF
You can thin the z-poxy with 99% isopropyl alcohol available at your local pharmacy. I have been thinning with this for years.
The ratio is 1:1:1. The beauty of using alcohol is that it thins but evaporates off without affecting the resin.
I would not not use the acetone for anything other than clean -up. Although I even use the alcohol for cleaning my epoxy brush.
Try not to use the 70% iso alcohol. Too much water.
The other advantage to iso alcohol is if you have any cuts on your hands they get disinfected - LOL!
ByronF
#8
Senior Member

Acetone is sold as an epoxy thinner. It says it right on the can of most brands.
If you do use drug store alcohol, get the stuff that has the highest percentage. The rest is water, and it gets trapped in the epoxy and weakens the final result. The water does not mix well and some is trapped as globules. It's known to leave swiss cheese like holes. Rubbing alcohol is false economy. Acetone, denatured alcohol, and pure isopropyl really doesn't cost much more. And acetone is made for the job. It's also good to have around. I've used more of it wiping up CA runs than thinning, especially since most finishing resin is almost brushing consistency when fresh.
If you do use drug store alcohol, get the stuff that has the highest percentage. The rest is water, and it gets trapped in the epoxy and weakens the final result. The water does not mix well and some is trapped as globules. It's known to leave swiss cheese like holes. Rubbing alcohol is false economy. Acetone, denatured alcohol, and pure isopropyl really doesn't cost much more. And acetone is made for the job. It's also good to have around. I've used more of it wiping up CA runs than thinning, especially since most finishing resin is almost brushing consistency when fresh.
#9
Senior Member
Thread Starter
Join Date: Dec 2001
Location: Queensland, AUSTRALIA
Posts: 525
Likes: 0
Received 0 Likes
on
0 Posts

Thanks guys for all the good info.
Here`s a progress report to date. Having read bandit driver`s post (#2 above) I decided to try a test panel. I used a flat panel with four layers of nylon and applied warmed epoxy that had also been thinned with a dash of acetone - less than 1-1-1. I left that out to harden in the sun - maybe 22*C, and it took nigh on 3 hours to even look like hardening. This morning, after about 24 hours I lifted and trimmed the panel. The mix had penetrated right through, no problem there, but the result result was rather like flexible hard leather rather than solid brittle hard....
Today I decided to bite the bullet and go for it for real. I left the resin and hardener out in the sun for about four hours and then mixed a conventional brew of two equal parts. I applied that to the four layers over the plug and worked it well through with a homemade foam brush - a strip of foam around 3" x 1" wrapped around a 1/2" x 1/8" spar offcut secured with a band of masking tape. I planned to do the job in two bites and just as well as the first lot hardened beyond further practical application when I was only about halfway through.
I finished that job about 3 hours ago and left it out in the sun to cure. Checked it just now and all is looking good. I`ll apply and sand one or two coats of sanding sealer before lifting it off the plug. I expect the finished article to be quite flexible if it is anything like previous efforts, but that won`t to be a problem with this small job. If it is, a band of 3/4 oz cloth epoxied around the inside will stiffen it nicely.
Thanks again.
Alan W
Here`s a progress report to date. Having read bandit driver`s post (#2 above) I decided to try a test panel. I used a flat panel with four layers of nylon and applied warmed epoxy that had also been thinned with a dash of acetone - less than 1-1-1. I left that out to harden in the sun - maybe 22*C, and it took nigh on 3 hours to even look like hardening. This morning, after about 24 hours I lifted and trimmed the panel. The mix had penetrated right through, no problem there, but the result result was rather like flexible hard leather rather than solid brittle hard....
Today I decided to bite the bullet and go for it for real. I left the resin and hardener out in the sun for about four hours and then mixed a conventional brew of two equal parts. I applied that to the four layers over the plug and worked it well through with a homemade foam brush - a strip of foam around 3" x 1" wrapped around a 1/2" x 1/8" spar offcut secured with a band of masking tape. I planned to do the job in two bites and just as well as the first lot hardened beyond further practical application when I was only about halfway through.
I finished that job about 3 hours ago and left it out in the sun to cure. Checked it just now and all is looking good. I`ll apply and sand one or two coats of sanding sealer before lifting it off the plug. I expect the finished article to be quite flexible if it is anything like previous efforts, but that won`t to be a problem with this small job. If it is, a band of 3/4 oz cloth epoxied around the inside will stiffen it nicely.
Thanks again.
Alan W
#10
Senior Member

Great idea that test.
Consider adding just a touch of acetone to get the best of both worlds.
BTW, finishing resin often contains waxes and components to improve the surface finish. They're not usually the resin of choice for structural stuff. (but that's in the real world)
Keep in mind that epoxy is often used in layups where flexibility is desired. White water kyaks showed up first in polyester resin but proved to be too brittle. The later epoxy boats proved to flex instead of crack. I heard it said that epoxy is like steel and polyster resin is like cast iron.
Consider adding just a touch of acetone to get the best of both worlds.
BTW, finishing resin often contains waxes and components to improve the surface finish. They're not usually the resin of choice for structural stuff. (but that's in the real world)
Keep in mind that epoxy is often used in layups where flexibility is desired. White water kyaks showed up first in polyester resin but proved to be too brittle. The later epoxy boats proved to flex instead of crack. I heard it said that epoxy is like steel and polyster resin is like cast iron.
#11
Senior Member

Where strength and dent resistance is important, refrain from using any type of thinner, especially alcohol. By far the best way is to use standard 30 minute or slower epoxy, spread it on as thin as you can then take a heat gun and evenly heat the area covered. Be careful not to get a spot so hot it bubbles, just 'til it starts to flow out. You will see the epoxy flow into the material giving complete wetting and penetration plus, it will now set up a little faster than if not heated. Any excess will also flow so that it can be wiped off with a paper towel. All thinners will degrade the quality of the end product.
#12

I thought the Z Poxy finishing resin didnt need to be thinned.. that it was made for glassing and had better flow characteristics built in and has a 60 min working time. I ask b/c I'm getting ready to glass my center section tomorrow and was going to give the Z Poxy resin a try this time instead of the 30 minute.??
#14
Senior Member
Thread Starter
Join Date: Dec 2001
Location: Queensland, AUSTRALIA
Posts: 525
Likes: 0
Received 0 Likes
on
0 Posts

Hi Mike,
I started this thread because I had a query concerning the viscosity, and thus usabilty of my Z-Poxy resin - was the thickness because of its old age and possible deterioration, or because of the cool temperature. Having since done the job I have come to the conclusion that the room temperature at the time caused my problem.
Based on my experience with Z- Poxy and other resins, I think you will find that the Z-Poxy will prove the better job for glassing your centre-section. Be aware that the warmer it is, the better it will flow or spread - but it will also go off quicker.
I don`t know the size of your wing, but I generally do this work in two bites - start with one panel of cloth on the underside and repeat the operation on the top after the first application has gone off.
Good luck,
Alan W
I started this thread because I had a query concerning the viscosity, and thus usabilty of my Z-Poxy resin - was the thickness because of its old age and possible deterioration, or because of the cool temperature. Having since done the job I have come to the conclusion that the room temperature at the time caused my problem.
Based on my experience with Z- Poxy and other resins, I think you will find that the Z-Poxy will prove the better job for glassing your centre-section. Be aware that the warmer it is, the better it will flow or spread - but it will also go off quicker.
I don`t know the size of your wing, but I generally do this work in two bites - start with one panel of cloth on the underside and repeat the operation on the top after the first application has gone off.
Good luck,
Alan W
#16
Junior Member
Join Date: Mar 2018
Posts: 1
Likes: 0
Received 0 Likes
on
0 Posts

I Used about 20% Alchohol to thin Z-Poxy 16 hrs later it's tacky? I looked on the internet and found this site I used 91% Isopropyl Alchohol to thin Z-Poxy 16 hrs later no much difference so I'm right now turned my oven on it's at 200 degrees I'm going to put my 3D Printed Doctor Who Tardis in for 20 mins if sticky another 20 mins and so on till it melts or Done? I'll let you know what happens O Ya its on a piece of 1/8" particle board, not metal it would melt!
#17

My Feedback: (3)

Sounds like you used Z-Poxy Epoxy as opposed to Z-Poxy Finishing Resin. Finishing Resin is much thinner and typically does not require thinning to spread nicely. It also cures to a harder finish. Thinning epoxy or finishing resin is never a great idea. But if you need to do so, Acetone is a much better thinner than Alcohol which can add water into the mix and does not flash off as quickly as Acetone. You can also warm the epoxy in a warm water bath but be aware it will cure much quicker so you have less working time.
Hope yours eventually cures but don't be surprised if it doesn't.
Hope yours eventually cures but don't be surprised if it doesn't.
#18
Moderator

The formulation is also different. Finishing resin is more aggressive in forming the polymer chains that make it harden because it's meant to cure when spread microscopically thin. Epoxy glue needs some thickness to cure as it's intended to be used thicker but also give you the working time you need.
On the original topic, I used a heat gun once to make finishing resin spread. I spread it as thin as I could, then heated it and carded it. It worked well with no thinning.
On the original topic, I used a heat gun once to make finishing resin spread. I spread it as thin as I could, then heated it and carded it. It worked well with no thinning.
#21

And while that is true for ELECTRICAL BONDING, it's not allowed for final cleaning in any application that involves application of sealants or adhesives. That's spelled out in black and white in several specification books at the major aerospace company I work at. Reason for it is IPA is made from plants and as such, when it evaporates, it leaves a residue that prevents proper adhesion of sealants and adhesives. What are allowed are methyl ethyl ketone(though it's heavily restricted), methyl propyl ketone and, in some cases, alphatic naptha or acetone.
Last edited by Hydro Junkie; 04-05-2018 at 09:40 PM.
#23

My Feedback: (29)

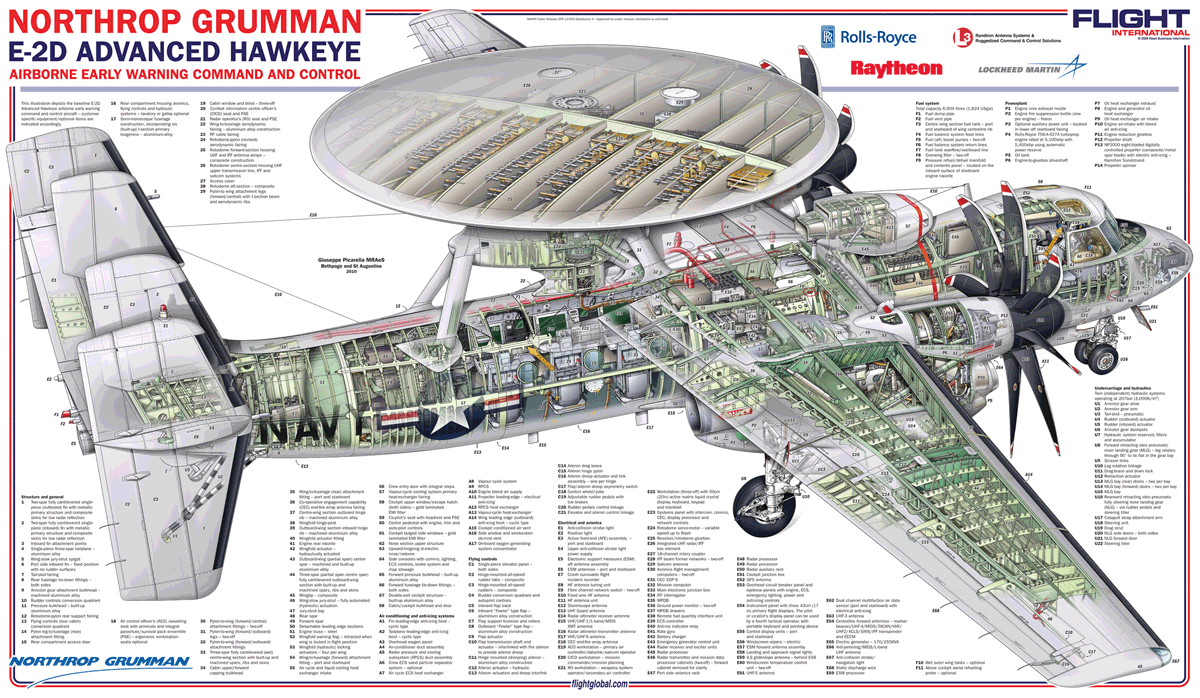
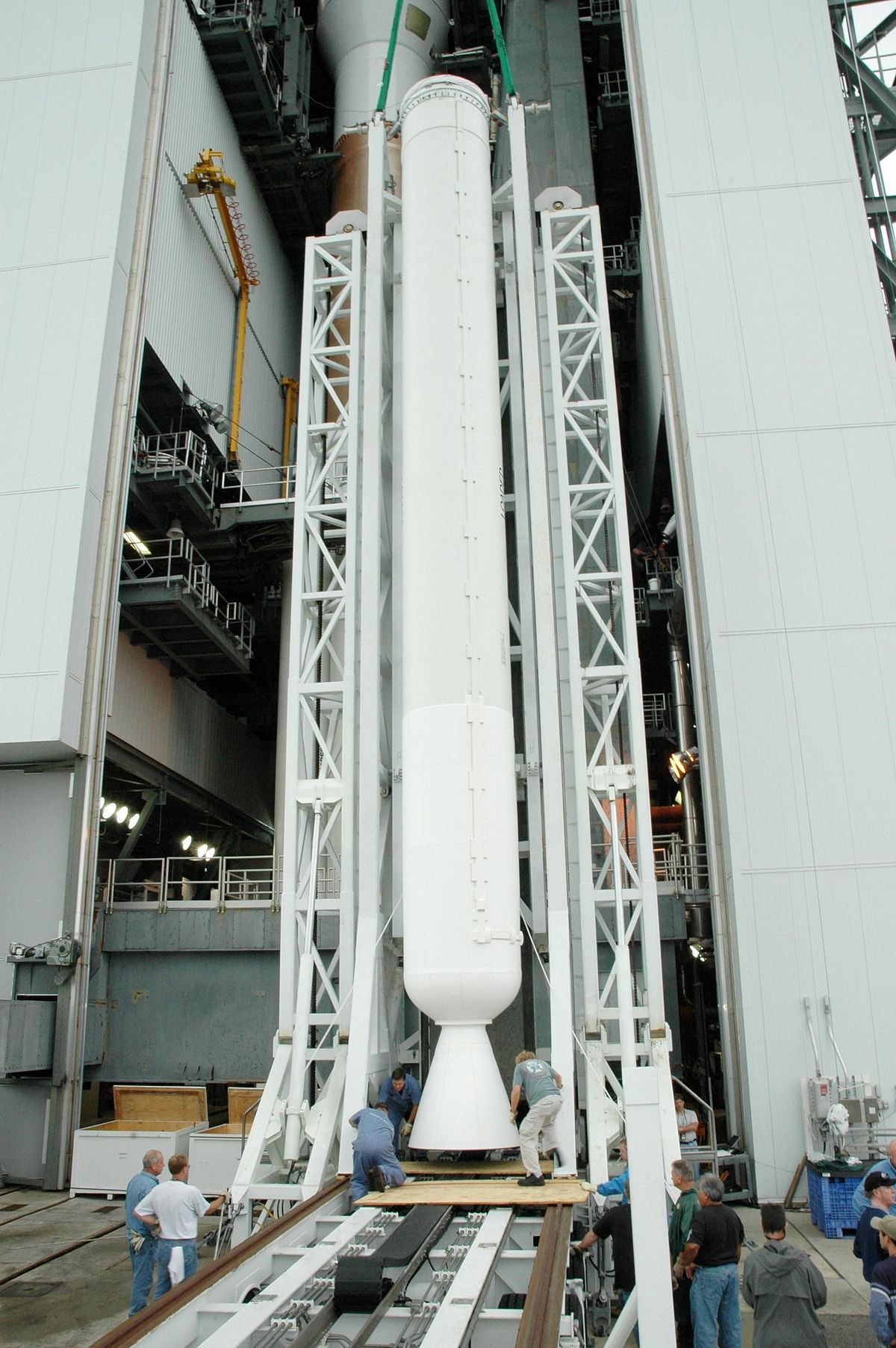
Here are a couple examples of hardware I have built using IPA as a cleaning solvent prior to bonding. In the case of the E2D royodome, you can see the section in the foreground has quite a few details bonded into the inner structure. While performing the bonds it is a rather tight space and IPA was chosen due to its lover vapor toxicity then Acetone. The Atlas SRB has a material bonded to it that would be damaged by the application of Acetone so again IPA was chosen. Mind you, for those processes we were not using off the shelf IPA and what was used may be a more refined version.
#24

My Feedback: (29)

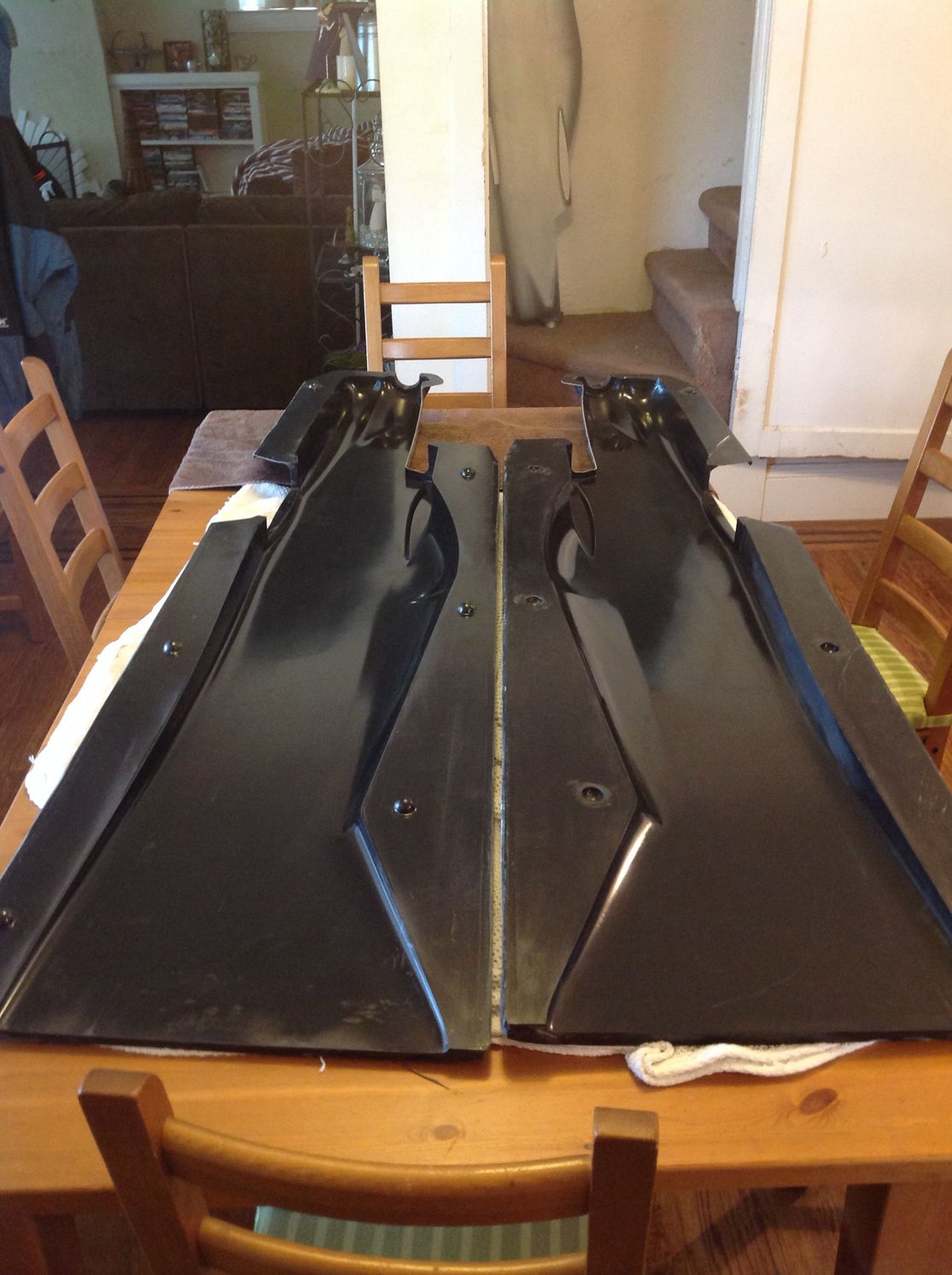
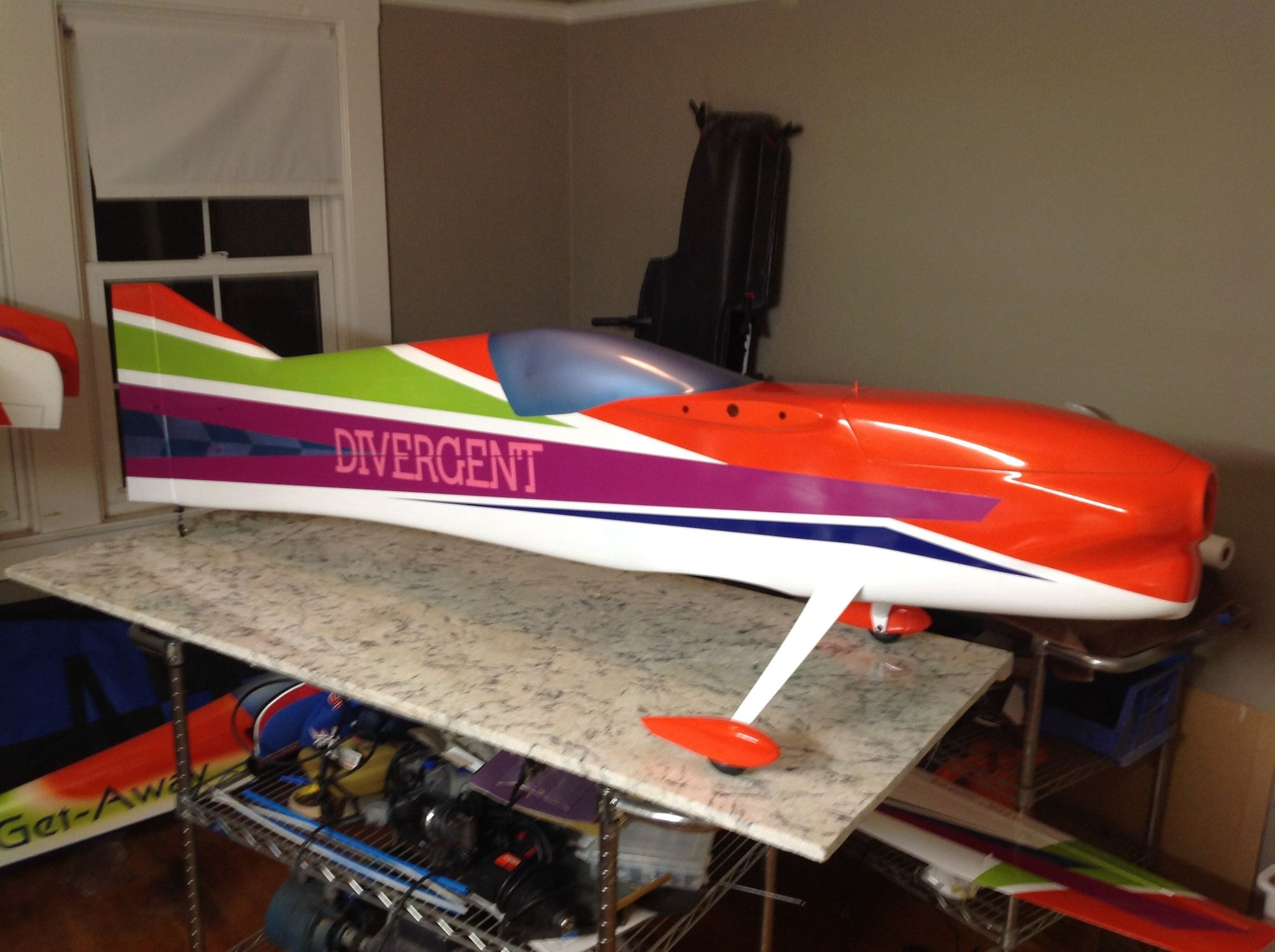
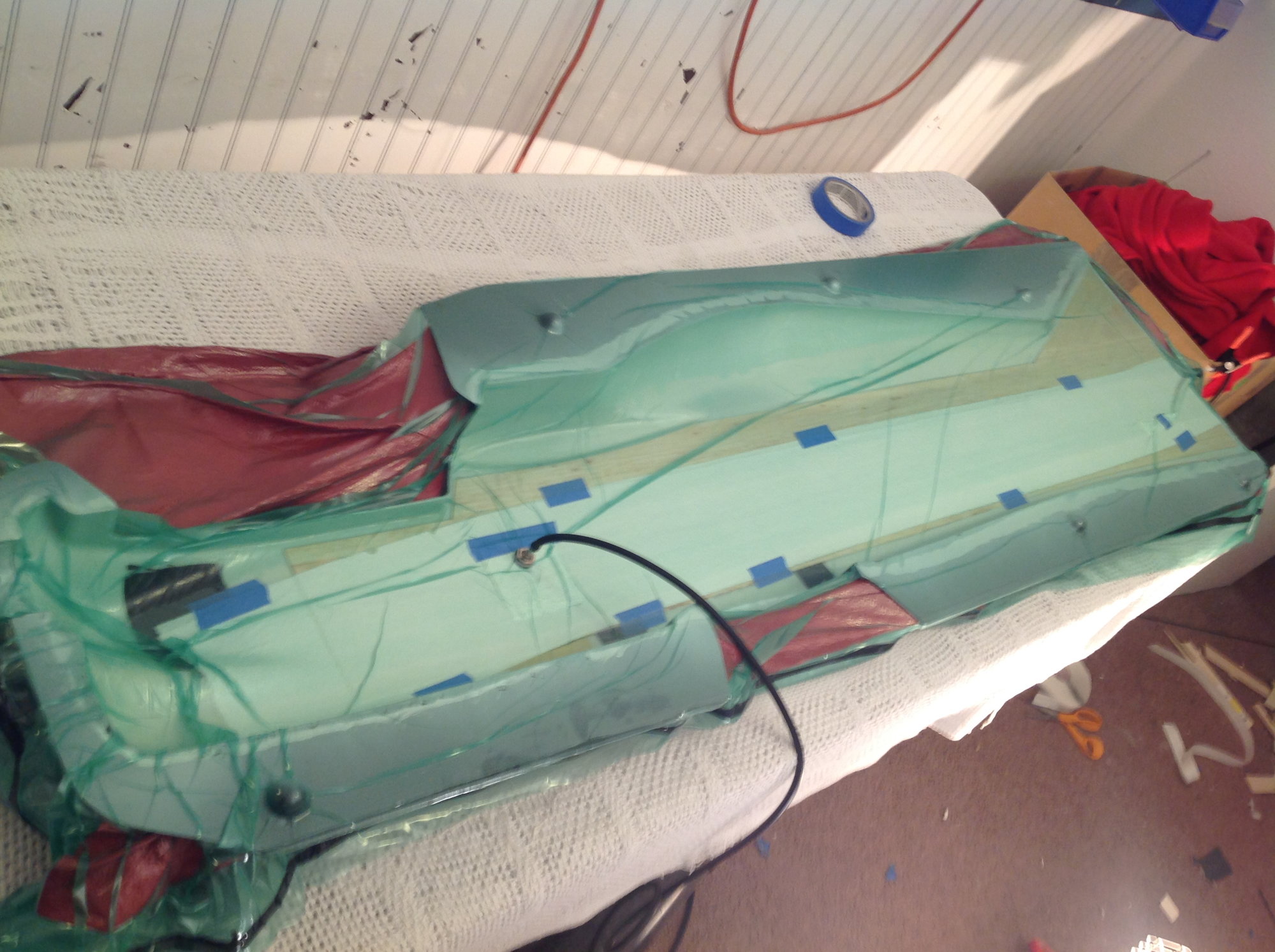
Now speaking of home projects. Here is a fuselage mold I recently finished. After the first few layers of surface cloth were applied, I thinned the laminating resin with IPA to extend the pot life and to get easier cloth saturation during then application of the bulk layers of cloth. Shown is the first fuselage to be pulled out of those molds.
Last edited by speedracerntrixie; 04-06-2018 at 06:04 AM.
#25

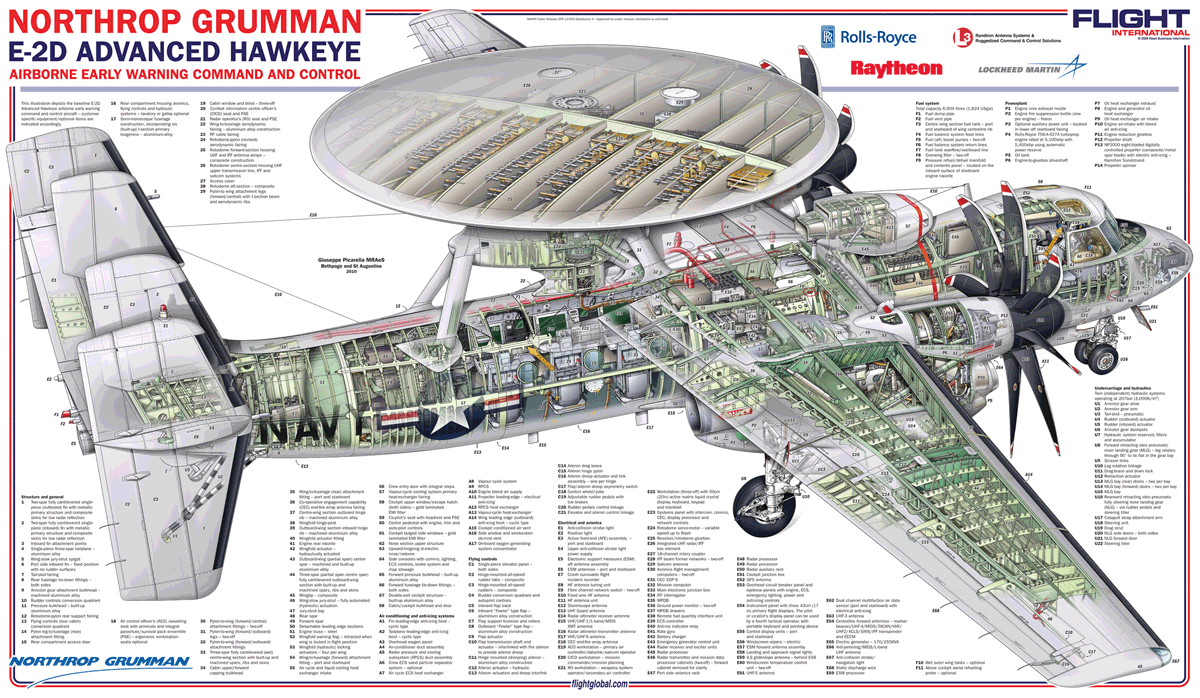
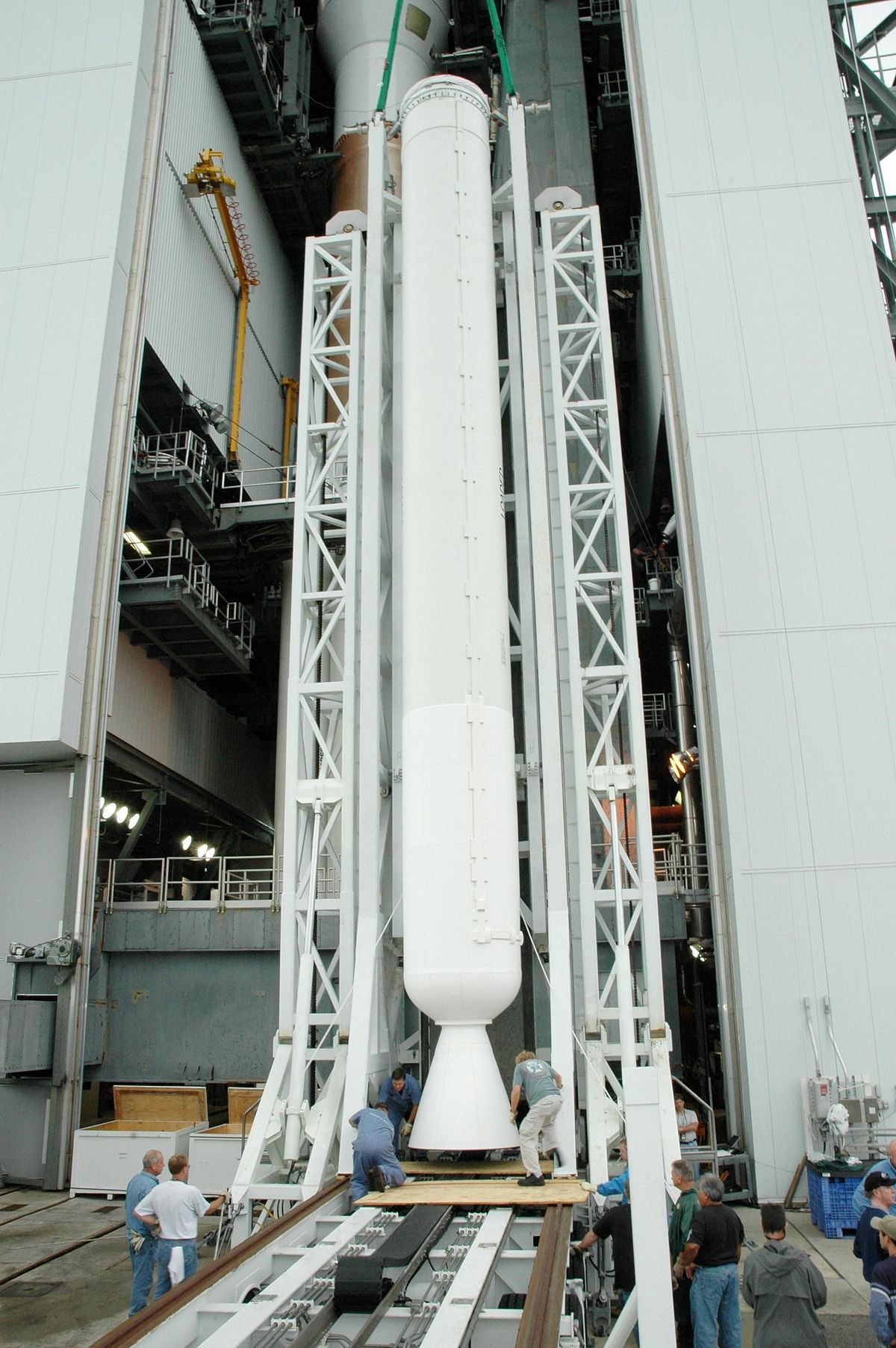
Here are a couple examples of hardware I have built using IPA as a cleaning solvent prior to bonding. In the case of the E2D royodome, you can see the section in the foreground has quite a few details bonded into the inner structure. While performing the bonds it is a rather tight space and IPA was chosen due to its lover vapor toxicity then Acetone. The Atlas SRB has a material bonded to it that would be damaged by the application of Acetone so again IPA was chosen. Mind you, for those processes we were not using off the shelf IPA and what was used may be a more refined version.